Exciting progress in the SOMMER project: Haldenwanger has developed new manufacturing routes for advanced materials that are essential for the ceramic membrane of the reactor.
Morgan Advanced Materials Haldenwanger GmbH is one of the industrial partners of the EU HORIZON founded SOMMER project. The project’s goal is to develop a novel carbon-neutral pathway for syngas production by integrating solar energy directly into a catalytic membrane reactor. A key component of the reactor is the functional ceramic membrane, which enables the splitting of H2O and CO2.
In close cooperation with Forschungszentrum (FZ) Jülich, Haldenwanger is screening different material systems for reactor conditions at 900 degrees Celsius and 1500 degrees Celsius. Their task is to adapt established manufacturing routes for promising membrane materials. The final shape of the ceramic membrane will be tubular.
First promising material selected
The first promising material for operation at 1500 degrees Celsius is CaO-FSZ, selected as a carrier material due to its proven high thermal resistance. Haldenwanger has developed an extrusion route for this material system. In extrusion, the material is continuously pushed through a die (a shaped opening) and hardens as it leaves the die, either through cooling or a chemical reaction.
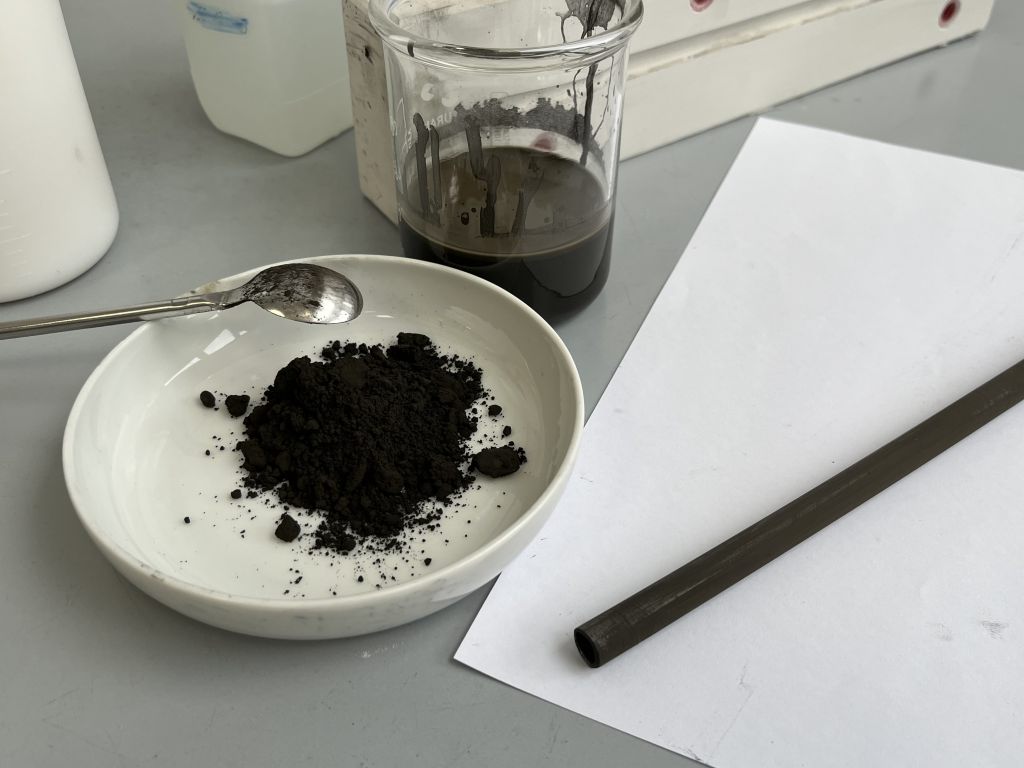
The key challenge is optimizing the formulation to ensure homogeneity and the right rheological properties (i.e. the material flow and deformation), while also fine-tuning the extrusion system parameters. By incorporating a burn-out pore-forming phase into the formulation, the project team successfully created tubes with a tailored porosity after the firing process. Haldenwanger manufactured a variety of porous structures by adjusting the size, morphology, and amount of the pore-forming phase. FZ Jülich will now use these porous tubes as a carrier material for a dip-coated dense functional layer to design an asymmetric membrane.
Developing a thin and dense membrane
A second approach for the solar reactor involves developing a thin and dense membrane. For this, STF (strontium titanate ferrite) has shown promising oxygen transport and catalytic properties for operation at 900 degrees Celsius. As part of the collaboration between science and industry in the SOMMER project, scientists and technicians from Haldenwanger and FZ Jülich are working together in the famous Haldenwanger laboratories to develop a slip casting method (using moulds) for manufacturing STF tubes. As a result of the first workshop, the team successfully produced 200 mm-long STF tubes. The next steps will focus on the optimization of wall thickness, mechanical strength and sintering process – the critical step of compacting and forming a solid mass of material.
Find out more about the consortium here.
Find out more about the project here.